We go behind the scenes at Native Instruments’ Berlin headquarters for an insight into the way the company develops new hardware.

Native Instruments’ Komplete Kontrol S
The life of an electronic instrument can be defined in three stages: the past, the present and the future.
The present is the easy one: that’s the part we all see, where the product is on sale. The future is of course the secretive part, with most manufacturers reluctant to reveal their plans for upgrades until they’re ready for release. It’s the past that we’re concerned with here. Like the proverbial tip of the iceberg, the product we see for sale is only the culmination of a much longer process, one which may have been taking place for years before it hits the market. Manufacturers rarely discuss it in detail, but instruments don’t just land in the shops out of nowhere; there’s typically a long and involved development process behind each one. When Native Instruments offered us the opportunity to find out more about how their Komplete Kontrol keyboard was developed and how the associated software system has evolved to the newly released version 1.8, we jumped at the chance.
Of course, very few musical instruments of any kind exist in isolation – whether hardware or software. Most relate in some way to legacy instruments or other products from the manufacturer’s current range. This is true in the case of NI, where the roots of the Reaktor software, for instance, stretch back to the early 90s, while other products such as Maschine, Komplete and Traktor all overlap to some extent.
We go through a product definition phase – research, ideation, validation, prototyping and testing – followed by a series of execution phases – engineering, prototyping, validation, production...
Hardware is a more recent development for NI, with the likes of their Traktor controllers and Maschine range arriving over the last decade. The Komplete Kontrol S-series is one of the more recent additions, designed initially as a bespoke controller keyboard for the Komplete package but developing into a broader product with the subsequent development of the Native Kontrol Standard software development kit.
The first we heard of Komplete Kontrol S was in late summer of 2014, when we were invited to NI’s London office to see a secret new product. By this point the unit was fully functional and ready for release, but as former industrial design team leader and current freelancer Adam Looker explains, work begins way in advance on this kind of project. “[The time scale] depends on a range of factors,” explains Looker, who studied industrial design in his native Canada before arriving at NI via various jobs in the audio, medical and environmental industries. “We go through a product definition phase – research, ideation, validation, prototyping and testing – followed by a series of execution phases – engineering, prototyping, validation, production…”

NI’s Matthias B, Dinos Vallianatos and Alexander Stamm testing the Komplete Kontrol S
With employees based in different departments and offices around the world, potentially working on multiple projects simultaneously, it’s important to manage the project carefully to ensure everyone moves efficiently in the right direction. This is further complicated by the fact that personnel can change over the course of a project and even the company structure and processes can change along the way. As Antonio Cardenas from the Komplete marketing team points out: “It’s an evolving matter. We thrive to become a lot better in every iteration.”
Each major project at NI is now driven by product managers and designers, responsible for overseeing the work and guiding the rest of the team. In the case of the Komplete Kontrol, some of that responsibility fell to London-based Tim Adnitt, a producer, composer and an NI employee since 2013. Adnitt joined the company around a year into the Komplete Kontrol project, when the hardware design was nearing completion and a software
Native Instruments has grown into a truly global brand, with outposts from Los Angeles to Tokyo, but product development still revolves around the company’s Berlin office, where most of the hardware and software development teams are based. The hardware development team alone contains industrial designers, user experience experts, mechanical engineers and electrical engineers. Once you add the software development teams, supply chain management teams, marketing teams and so on, there are dozens of people involved in any given project.

A stress and fatigue tester analysing the durability of physical components
The original ideas behind the Komplete Kontrol project go back many years. Senior product manager Matthias B explains that the viability of any new project is rooted in user feedback. “We are constantly in touch with our users around the world,” he says, “in order to verify our ideas and assumptions around new product concepts and to understand their needs and pain points.” Matthias, who has been at NI for four years having previously worked for companies including Digidesign, Avid and inMusic, stresses the importance of involving users in interviews, surveys and hands-on tests to explore potential new products. “We also work closely with our market research department to understand the market in general and how it is changing,” he adds.
With the decision made to explore the keyboard idea, the design work could begin in earnest. No individual could claim all the credit for the team’s work, but Dinos Vallianatos played one of the most important roles in its creation. Greek-born Vallianatos joined NI in 2009 as a sound designer and has since worked his way up the ladder to product owner for Kontakt, but in the interim he held the position of senior product designer on the Komplete Kontrol project. “We started as a small group of people having a number of ideas on what a Komplete keyboard could look like,” he explains. “My job was to shape different versions of putting these ideas together into a single product that is feasible to develop and manufacture.”
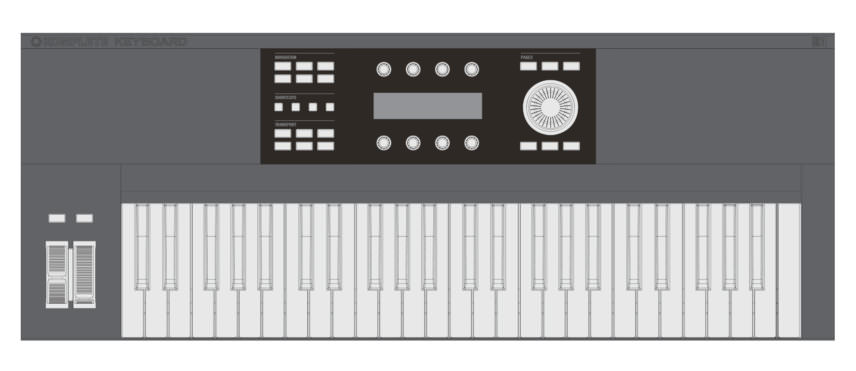
A very early layout design for what was then known as the Komplete Keyboard
NI have been aware of public demand for a keyboard for some time, but everyone we speak to at the company makes it clear that creating an identikit MIDI controller was never an option. Vallianatos in particular is unequivocal that Komplete Kontrol should be considered an instrument in its own right rather than a controller. “It was designed from the ground up to be an instrument,” he explains. “Pressing or turning anything on it yields a clear audible or visible response that musicians don’t have to set up beforehand. You know, like a piano or a guitar! Generic controllers are great if you actually need one, and Komplete Kontrol can also be that if you want it to. But by being generic and trying to serve every possible user need, often including every possible combination of controls, there is no way around ending up with most controls just sitting there never being used.”
As an outsider to the process, I find this point particularly important. When reviewing gear, I’m often guilty of pointing out missing features or options which could have been added; speaking to the NI team makes me understand much better why adding more features doesn’t necessarily improve a piece of equipment. Not only does the complexity rise, but so does the product cost. As such, every design decision has an impact on the final cost of the product, as Looker explains: “The various costs and features have to be weighed against the benefit to the user. Of course everybody wants the best looking product with the most expensive materials, features and finishes, but when the affordability of the product drops significantly, then we aren’t properly addressing the needs of our customers.”
Of course everybody wants the best looking product with the most expensive materials, features and finishes, but when the affordability of the product drops significantly, then we aren’t properly addressing the needs of our customers.
What quickly becomes apparent when talking to the NI team is how analytical everyone is. This probably shouldn’t come as a surprise, but it’s still hard not to be taken aback by the thoughtfulness and open-minded approach. This is reinforced when the designers recall one early meeting in which there was a brief discussion about whether the keyboard could include a built-in cup holder or ashtray. They’re joking, of course, but you get the impression that even these tongue-in-cheek suggestions reflect an anything-goes approach, in which everything can be questioned at any stage. Matthias explains that nothing is ever set in stone during the design phase, with everything open to discussion: “After having worked at other companies within the industry, what still impresses me most about NI is that we’re not afraid to go back to the drawing board and to start from scratch, until we get it right. Releasing halfbaked products is not our style. We want it to be as good as technically possible.”

Light Guide elements being tested
The final design for Komplete Kontrol manages to combine simplicity with a number of unique touches. Looker admits that some of the early ideas became overly complicated: “It became really complex and a bit too radical, so we dialled it back into something a bit more focussed.” The end result may not be as complex as some earlier designs, but there are still a number of innovative ideas packed in, from the Light Guide which offers visual feedback on mappings and instruments, to the modulation touch strips and the Smart Play features for scales, chords and arps.
It would probably be a stretch to describe the manufacturing process as the easy part, but I do get a sense that with the fully formed idea in place, the rest is a matter of going through an established process of prototyping and testing. There are, of course, entirely new elements included in the Komplete Kontrol, but the company’s experience of developing hardware in the form of Traktor Kontrols and Maschines surely gives them a good understanding of how to translate those designs into finished products. From an industrial design perspective, Looker notes that entirely new features such as the Light Guide elements and the ultra-black displays presented the biggest challenges. In addition to the hardware elements themselves, the latter required the creation of a custom font, which I confess is a part of the design process I’d never even considered until it was pointed out to me.

The internal workings of the KKS keyboard
By the time the Komplete Kontrol hit the market in 2014, thousands of man hours had been invested in its development. Designs had been tweaked and refined, every electronic component specified and sourced. The physical appearance had been developed from 2D sketches and life-sized printouts of the panel through to CAD drawings and extensively tested 3D prototypes (one mechanical engineer even walked across a unit suspended between two keyboard stands in order to prove the rigidity of the housing). I suggest to Alexander Stamm, the head of marketing for Komplete, that this must be time for him to get involved in the process, but of course he’s way ahead of me: the marketing team are involved from the very beginning, working collaboratively with the other team members from the ideation stage.
Ultimately, Stamm argues, “the best marketing is done by having great products.” Everyone we speak to agrees that the most satisfying part of the process comes after the product is finished, when they finally get to release it to the public and see how musicians react to it. As Looker puts it: “Seeing artists performing and enjoying the end product is incredibly rewarding. For example, seeing photos of Hans Zimmer enjoying playing the Komplete Kontrol S61 was really great.”

Trial fitting touch strip components
Having been so forthcoming when discussing the roots of the project, the team become slightly more tight-lipped when we ask about the future development plans for Komplete Kontrol and the associated Native Kontrol Standard (NKS). Adnitt explains that future plans for an existing product may extend years into the future. As an example of the commitment to ongoing development he’s keen to point out the expansion of accessibility features in the Komplete Kontrol 1.8 update: “It continues to build on the accessibility features for visually-impaired musicians and producers. The new additions to Scale, Chord and Transport have all been designed from the beginning with accessibility in mind.”
Matthias hints that the team are particularly interested in developing the NKS even further. The NKS is a software development kit that makes it possible for third-party plugins and Kontakt instruments to integrate with Komplete Kontrol software and hardware on the exact same level as NI’s own instruments. The system has already been adopted by companies including Arturia, U-he and Spitfire, providing a consistent experience across the board for Komplete users.
The NKS opens the Komplete Kontrol system to all third-party instrument developers... For the user it is great, because we can provide a really consistent user experience.
“The NKS opens the Komplete Kontrol system to all third-party instrument developers,” Matthias explains. “The integration goes beyond instrument parameter mapping for the Komplete Kontrol keyboards, but also provides deep integration with Maschine. To date more than 170 NKS instruments from 50 different partners are already available on our NKS platform, and the number keeps growing every month. For the user it is great, because we can provide a really consistent user experience, whether it is the browser, the sound parameter mapping, or the Smart Play features and the Light Guide.” With developers including Arturia, Waldorf and U-he already adopting the protocol, it’ll be interesting to see how far that integration of hardware and software can go.
While they may not be willing to reveal too much about what’s coming next, we’re confident there are teams already hard at work on the next round of features. We may not see them for months or even years, but you can be sure that somewhere behind a locked door in Berlin, people are also busy creating NI’s next generation of instruments. Cup holders may or may not feature.